Finalidade dos materiais de revestimento
Revestir a superficie externa das tubaxes de aceiro é crucial para evitar a oxidación. A oxidación na superficie das tubaxes de aceiro pode afectar significativamente a súa funcionalidade, calidade e aspecto visual. Polo tanto, o proceso de revestimento ten un impacto considerable na calidade xeral dos produtos de tubaxes de aceiro.
-
Requisitos para os materiais de revestimento
Segundo as normas establecidas polo Instituto Americano do Petróleo, as tubaxes de aceiro deben resistir a corrosión durante polo menos tres meses. Non obstante, a demanda de períodos antioxidantes máis longos aumentou, e moitos usuarios requiren resistencia de 3 a 6 meses en condicións de almacenamento ao aire libre. Ademais do requisito de lonxevidade, os usuarios esperan que os revestimentos manteñan unha superficie lisa e unha distribución uniforme dos axentes anticorrosivos sen salpicaduras nin goteos que poidan afectar á calidade visual.
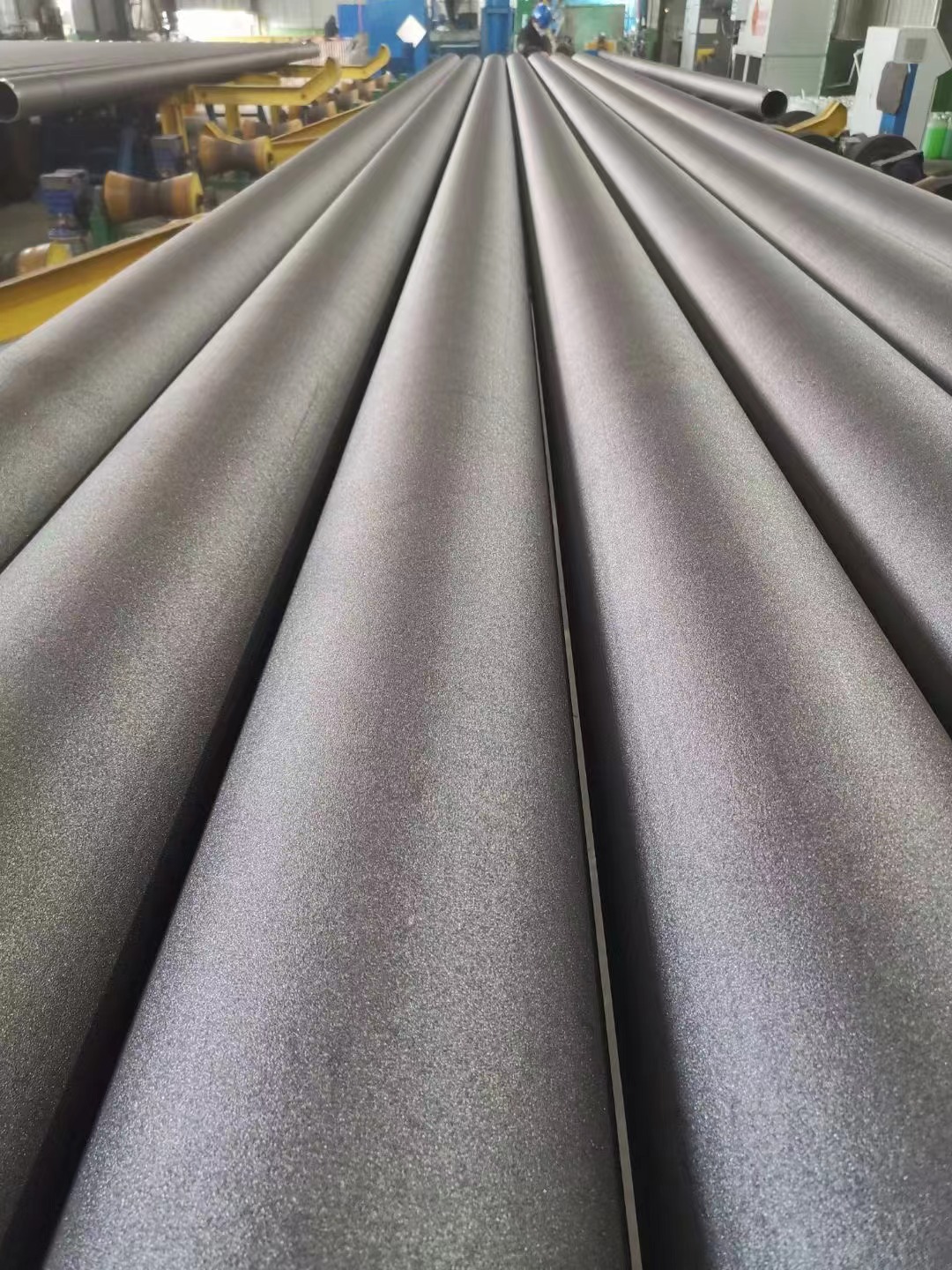
-
Tipos de materiais de revestimento e as súas vantaxes e desvantaxes
Nas redes urbanas de tubaxes subterráneas,tubos de aceiroúsanse cada vez máis para transportar gas, petróleo, auga e moito máis. Os revestimentos destas tubaxes evolucionaron desde os materiais asfálticos tradicionais ata a resina de polietileno e os materiais de resina epoxi. O uso de revestimentos de resina de polietileno comezou na década de 1980 e, con diversas aplicacións, os compoñentes e os procesos de revestimento experimentaron melloras graduais.
3.1 Revestimento de asfalto de petróleo
O revestimento de asfalto de petróleo, unha capa anticorrosiva tradicional, consiste en capas de asfalto de petróleo reforzadas con tea de fibra de vidro e unha película protectora externa de cloruro de polivinilo. Ofrece unha excelente impermeabilización, boa adhesión a diversas superficies e rendibilidade. Non obstante, ten inconvenientes, como a susceptibilidade aos cambios de temperatura, a súa fragilidade a baixas temperaturas e a súa tendencia ao envellecemento e ao rachado, especialmente en solos rochosos, o que require medidas de protección adicionais e un aumento dos custos.
3.2 Revestimento epoxi de alcatrán de hulla
O epoxi de alcatrán de hulla, feito de resina epoxi e asfalto de alcatrán de hulla, presenta unha excelente resistencia á auga e aos produtos químicos, á corrosión, boa adhesión, resistencia mecánica e propiedades de illamento. Non obstante, require un tempo de curado máis longo despois da aplicación, o que o fai susceptible aos efectos adversos das condicións meteorolóxicas durante este período. Ademais, os diversos compoñentes utilizados neste sistema de revestimento necesitan un almacenamento especializado, o que aumenta os custos.
3.3 Revestimento en po epoxi
O revestimento en po epoxi, introducido na década de 1960, consiste en pulverizar electrostaticamente po sobre superficies de tubaxes pretratadas e prequentadas, formando unha densa capa anticorrosiva. As súas vantaxes inclúen un amplo rango de temperaturas (de -60 °C a 100 °C), unha forte adhesión, unha boa resistencia á desvinculación catódica, aos impactos, á flexibilidade e aos danos nas soldaduras. Non obstante, a súa película máis fina faino susceptible a danos e require técnicas e equipos de produción sofisticados, o que supón desafíos na aplicación no campo. Aínda que destaca en moitos aspectos, non é o axeitado para o polietileno en termos de resistencia á calor e protección xeral contra a corrosión.
3.4 Revestimento anticorrosivo de polietileno
O polietileno ofrece unha excelente resistencia ao impacto e unha alta dureza, xunto cun amplo rango de temperaturas. Ten un uso amplo en rexións frías como Rusia e Europa Occidental para tubaxes debido á súa flexibilidade e resistencia ao impacto superiores, especialmente a baixas temperaturas. Non obstante, segue habendo desafíos na súa aplicación en tubaxes de gran diámetro, onde poden producirse fisuras por tensión e a entrada de auga pode provocar corrosión debaixo do revestimento, o que fai necesaria máis investigación e melloras nos materiais e nas técnicas de aplicación.
3.5 Revestimento anticorrosivo pesado
Os revestimentos anticorrosión pesados ofrecen unha resistencia á corrosión significativamente mellorada en comparación cos revestimentos estándar. Presentan unha eficacia a longo prazo mesmo en condicións adversas, con vidas útiles que superan os 10 a 15 anos en ambientes químicos, mariños e con solventes, e de máis de 5 anos en condicións ácidas, alcalinas ou salinas. Estes revestimentos adoitan ter grosores de película seca que oscilan entre os 200 μm e os 2000 μm, o que garante unha protección e durabilidade superiores. Úsanse amplamente en estruturas mariñas, equipos químicos, tanques de almacenamento e tubaxes.
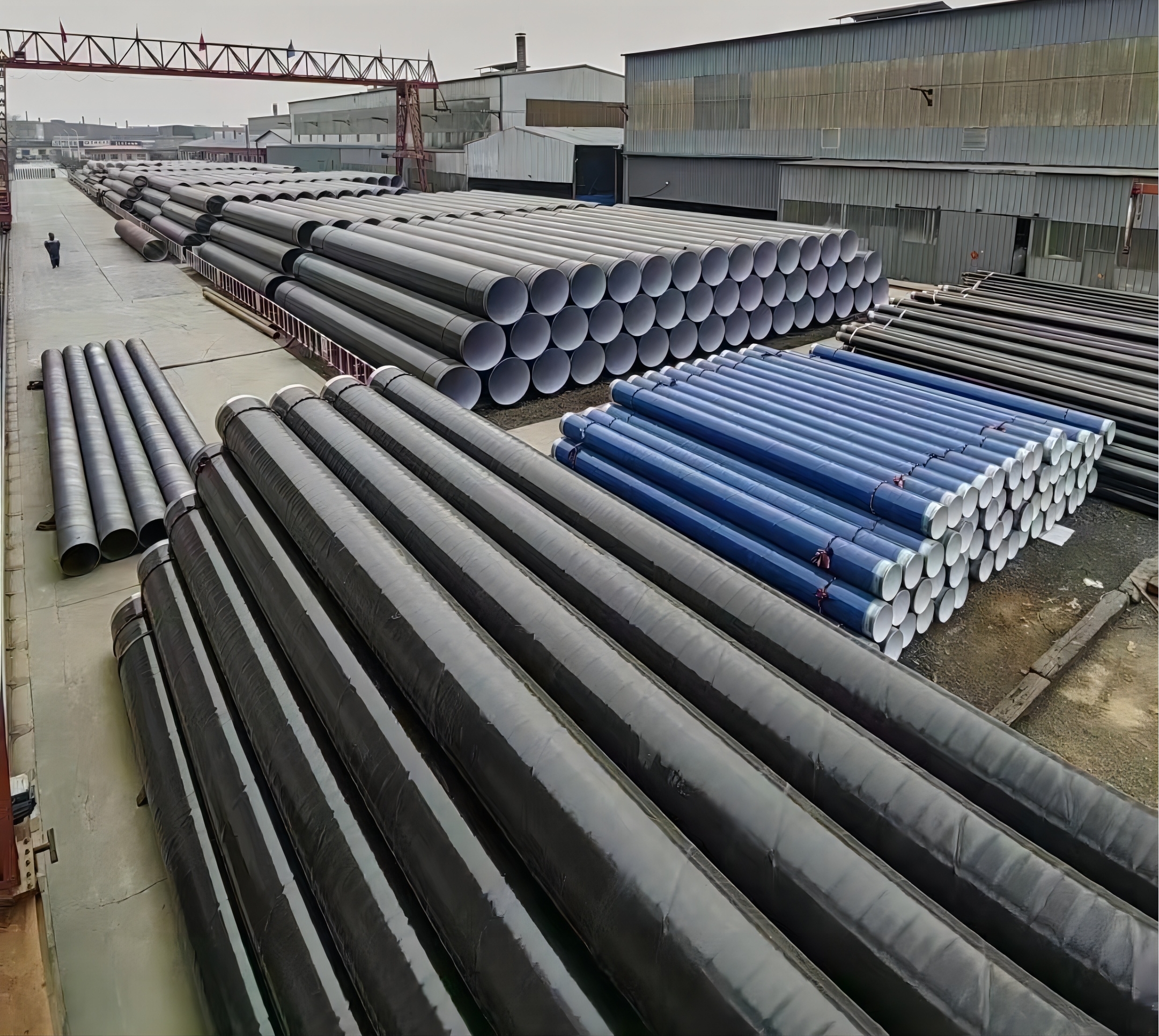
-
Problemas comúns cos materiais de revestimento
Entre os problemas comúns cos revestimentos inclúense a aplicación irregular, o goteo de axentes anticorrosivos e a formación de burbullas.
(1) Revestimento desigual: Unha distribución desigual dos axentes anticorrosivos na superficie da tubaxe produce zonas cun grosor de revestimento excesivo, o que provoca desperdicios, mentres que as zonas finas ou sen revestimento reducen a capacidade anticorrosiva da tubaxe.
(2) Pingas de axentes anticorrosivos: este fenómeno, no que os axentes anticorrosivos solidifican en forma de pingas na superficie da tubaxe, inflúe na estética sen afectar directamente á resistencia á corrosión.
(3) Formación de burbullas: O aire atrapado no axente anticorrosivo durante a aplicación crea burbullas na superficie da tubaxe, o que afecta tanto á aparencia como á eficacia do revestimento.
-
Análise de problemas de calidade de revestimento
Cada problema xorde por unha variedade de razóns, está causado por unha variedade de factores; e un feixe de tubos de aceiro destacado pola calidade do problema tamén pode ser unha combinación de varios. As causas do revestimento desigual pódense dividir aproximadamente en dous tipos, un é o fenómeno desigual causado pola pulverización despois de que o tubo de aceiro entre na caixa de revestimento; o segundo é o fenómeno desigual causado pola falta de pulverización.
A razón do primeiro fenómeno é obviamente doada de ver: cando o equipo de revestimento introduce o tubo de aceiro na caixa de revestimento en 360°, hai un total de 6 pistolas (a liña de revestimento ten 12 pistolas) para pulverizar. Se o tamaño do fluxo de cada pistola pulverizada é diferente, isto provocará unha distribución desigual do axente anticorrosivo nas distintas superficies do tubo de aceiro.
A segunda razón é que existen outras razóns para o fenómeno do revestimento desigual ademais do factor de pulverización. Hai moitos tipos de factores, como a ferruxe entrante do tubo de aceiro, a rugosidade, de xeito que o revestimento é difícil de distribuír uniformemente; a superficie do tubo de aceiro ten unha medición da presión da auga que queda cando a emulsión, esta vez para o revestimento debido ao contacto coa emulsión, de xeito que o conservante é difícil de adherir á superficie do tubo de aceiro, de xeito que non hai revestimento das partes do tubo de aceiro da emulsión, o que resulta en que o revestimento de todo o tubo de aceiro non sexa uniforme.
(1) A razón pola que o axente anticorrosivo cae en suspensión. A sección transversal do tubo de aceiro é redonda, cada vez que se pulveriza o axente anticorrosivo sobre a superficie do tubo de aceiro, o axente anticorrosivo da parte superior e do bordo fluirá cara á parte inferior debido ao factor de gravidade, o que formará o fenómeno da caída en suspensión. O bo é que hai equipos de forno na liña de produción de revestimento da fábrica de tubos de aceiro, que poden quentar e solidificar o axente anticorrosivo pulverizado sobre a superficie do tubo de aceiro co tempo e reducir a fluidez do axente anticorrosivo. Non obstante, se a viscosidade do axente anticorrosivo non é alta; non se quenta a tempo despois da pulverización; ou a temperatura de quecemento non é alta; a boquilla non está en bo estado de funcionamento, etc., provocará que o axente anticorrosivo caia en suspensión.
(2) Causas da formación de escuma anticorrosiva. Debido á humidade do aire no ambiente de operación, a dispersión excesiva da pintura, a caída da temperatura do proceso de dispersión provocará o fenómeno de burbullas do conservante. A humidade do aire no ambiente e as condicións de temperatura máis baixas provocan a pulverización de conservantes que se dispersan en pequenas pingas, o que provocará unha caída da temperatura. A auga do aire con maior humidade, despois da caída da temperatura, condensarase para formar pingas finas mesturadas co conservante e, finalmente, entrará no interior do revestimento, o que provocará a formación de burbullas no revestimento.
Data de publicación: 15 de decembro de 2023